Réalisations laser #1 : 40 % d’économie grâce à la soudure laser
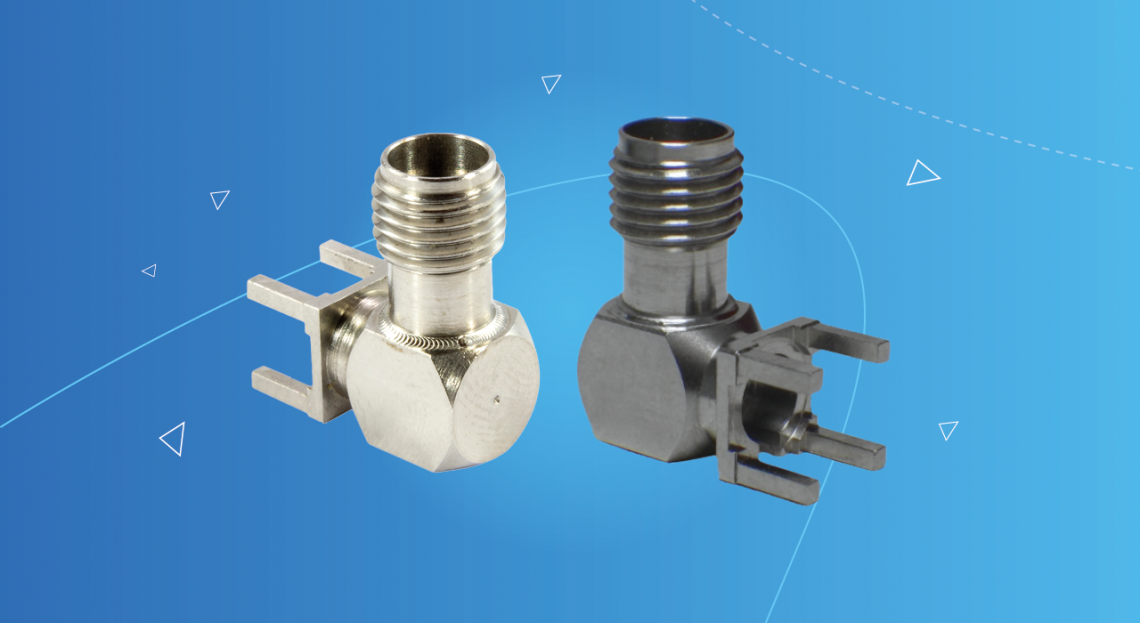
Après avoir mis en lumière les multiples expertises nécessaires au bon déroulement d’un projet de soudage laser, et exploré la diversité de métaux et alliages compatibles avec ce type d’opération, explorons ensemble les réalisations fondamentales de nos équipes. La première de la série ? Le coude SMA – ou comment le passage du brasage de métaux à la soudure a entraîné une économie significative de 40 %.
Le contexte d’un tel projet
Nous sommes dans les années 1990, au Salon international de l’aéronautique et de l’espace du Bourget. Nous y rencontrons un acteur majeur de la télécommunication, un client en devenir.
Le sujet de discussion ? Le coude, formé de deux pièces et mesurant seulement 1 cm sur 1 cm. Un composant qui revêt une importance cruciale en raison de son utilisation comme renvoi d’angle haute fréquence pour la connectique.
Un défi de taille
La matière utilisée pour concevoir ce coude, c’est l’inox AISI 303. Or, ce type d’inox, dit de décolletage à haute teneur en soufre, présente un risque de fissuration à chaud très important.
Pour assembler ces pièces, notre client avait recours à la brasure – une technique impliquant l’ajout d’un métal extérieur (ici, une base cuivreuse) pour joindre les deux pièces. Cette méthode, bien que répandue, présente de nombreux défauts et demande des améliorations et retouches fréquentes. C’est le cas de la soudure entre titane et inox, qui est encore sujette à des recherches actives, notamment menées par les équipes de Laser Rhône Alpes.
Un coude et des enjeux bien définis
Les multiples enjeux de notre client ont guidé nos recherches :
- Comment gagner du temps d’usinage ?
- Peut-on industrialiser le processus de fabrication en limitant les retouches ?
- Par rapport à la brasure, est-il possible de faire des économies sur les coûts de mise en œuvre ?
Pour y répondre, nous avions plusieurs avantages : la bonne technologie et la proximité.
« C’est une entreprise de la région Auvergne Rhône-Alpes, nous sommes donc voisins. C’était un atout pour nos équipes respectives dans ce projet de recherche. »
Michel Almuneau, responsable technique chez Laser Rhône Alpes
La mise en œuvre du projet
Avec notre client, nous avons conjointement œuvré à la recherche du bon design des pièces et à la définition de méthodes de fixation pour le soudage – notamment pour savoir comment maintenir les pièces ensemble avant de les souder. Nous sommes passés d’un assemblage glissant à un autre par sertissage avant le soudage laser. Un changement qui a demandé de tester de nombreuses séries de quelques centaines de pièces chacune, avant de déterminer le processus optimal.
La cadence de soudage est passée à près de 20 000 pièces par mois, ce qui a exigé une semi-automatisation du process :
- positionner la pièce,
- réaliser la soudure,
- ranger la pièce.
Cette semi-automatisation a considérablement réduit le temps nécessaire à chaque opération. En tout, deux ans de recherches et de développement ont été nécessaires pour parvenir à cette solution.
« Nous sommes partis d’une page blanche et, ensemble, nous avons trouvé le bon design et la bonne technologie. À noter qu’au début des années 1990, seul le laser pulsé existait, ce qui entraînait quelques rebuts dus à la fissuration à chaud.
En 1996, LRA a fait l’acquisition du premier laser continu en France utilisé en sous-traitance. Une nouvelle technologie qui a permis d’améliorer la qualité de l’opération, réduisant presque entièrement les défauts de fissuration à chaud que nous rencontrions auparavant. »
Michel Almuneau, responsable technique chez Laser Rhône Alpes
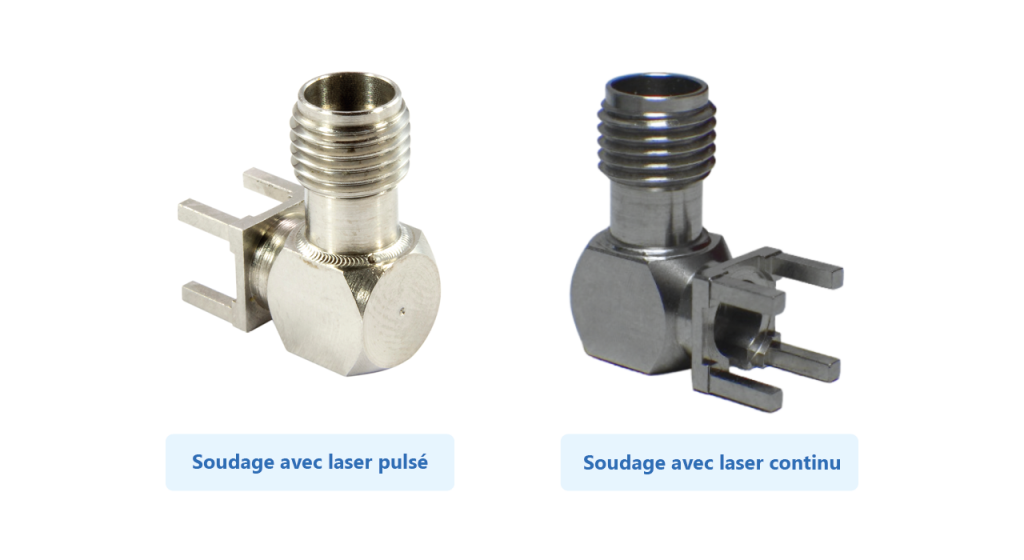
Résultat : 40 % d’économie
La soudure laser a apporté des résultats significatifs. L’un des deux demi-corps a été remplacé par une pièce standard, tandis que l’autre a été personnalisé selon les besoins spécifiques, réduisant ainsi le besoin de retouches et facilitant la mise en œuvre.
D’un point de vue financier, pour des quantités de plusieurs milliers de pièces, les coûts de mise en œuvre se sont avérés plus compétitifs par rapport à la brasure, avec environ 40 % d’économies.
35 ans après sa reconception, le coude SMA est toujours soudé avec expertise par l’équipe de Laser Rhône Alpes. Ce type de réalisation vous intéresse ?

